In-Situ
Proposal for the NASA 3-d Printed Habitat Design Challenge
Mars, 2015
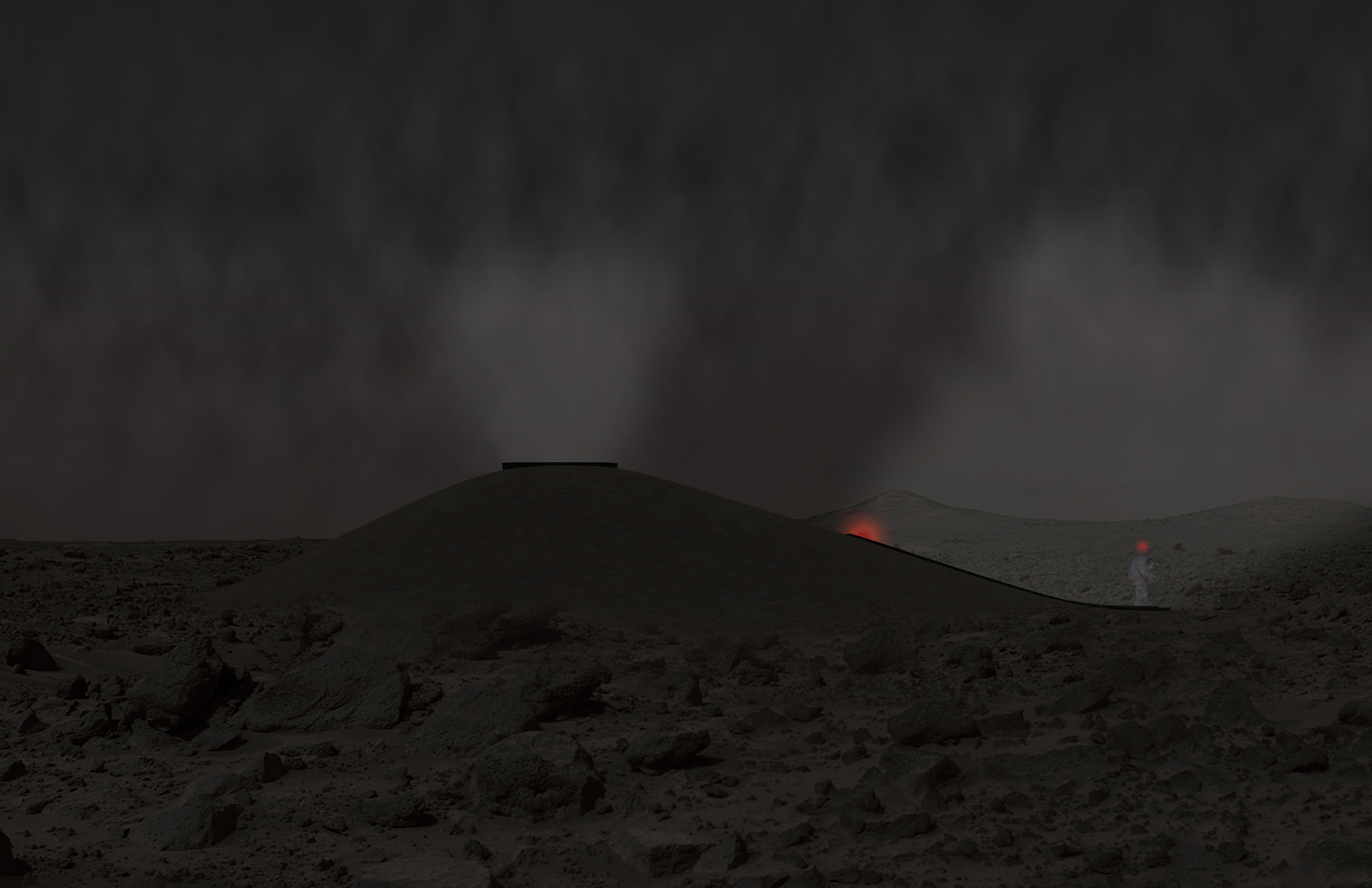
While the construction of a building on mars, 140 million miles from earth, is objectively the ultimate trial of utility, restraint, and efficiency, it also represents the instantaneous actuation of the next era of architectural design, and therefore must comprehensively embody the essence of a new paradigm in assembly, composition, and form. The extreme cost of transporting materials from Earth to Mars and the ingrained inefficiencies and waste associated with terrestrial construction necessitate an additive manufacturing technique that exclusively uses in-situ building materials. Fully-automated 3d printing eliminates the need to account for human error, the tolerances necessitated by trade work, and reliance upon prefabricated rectilinear building components. Thus, our proposal for the design and assembly of a habitat on Mars employs an advanced single-process solar laser-based additive manufacturing process, using Martian surface dust and carbon harnessed from Mars’ atmosphere, to yield an extremely efficient structure that is formally influenced by mathematically derived minimal surfaces and molecular geometry. The proposed process and product will minimize energy use, protect its inhabitants from solar radiation, and allow them to live and work comfortably for the duration of their extra-terrestrial exploration.
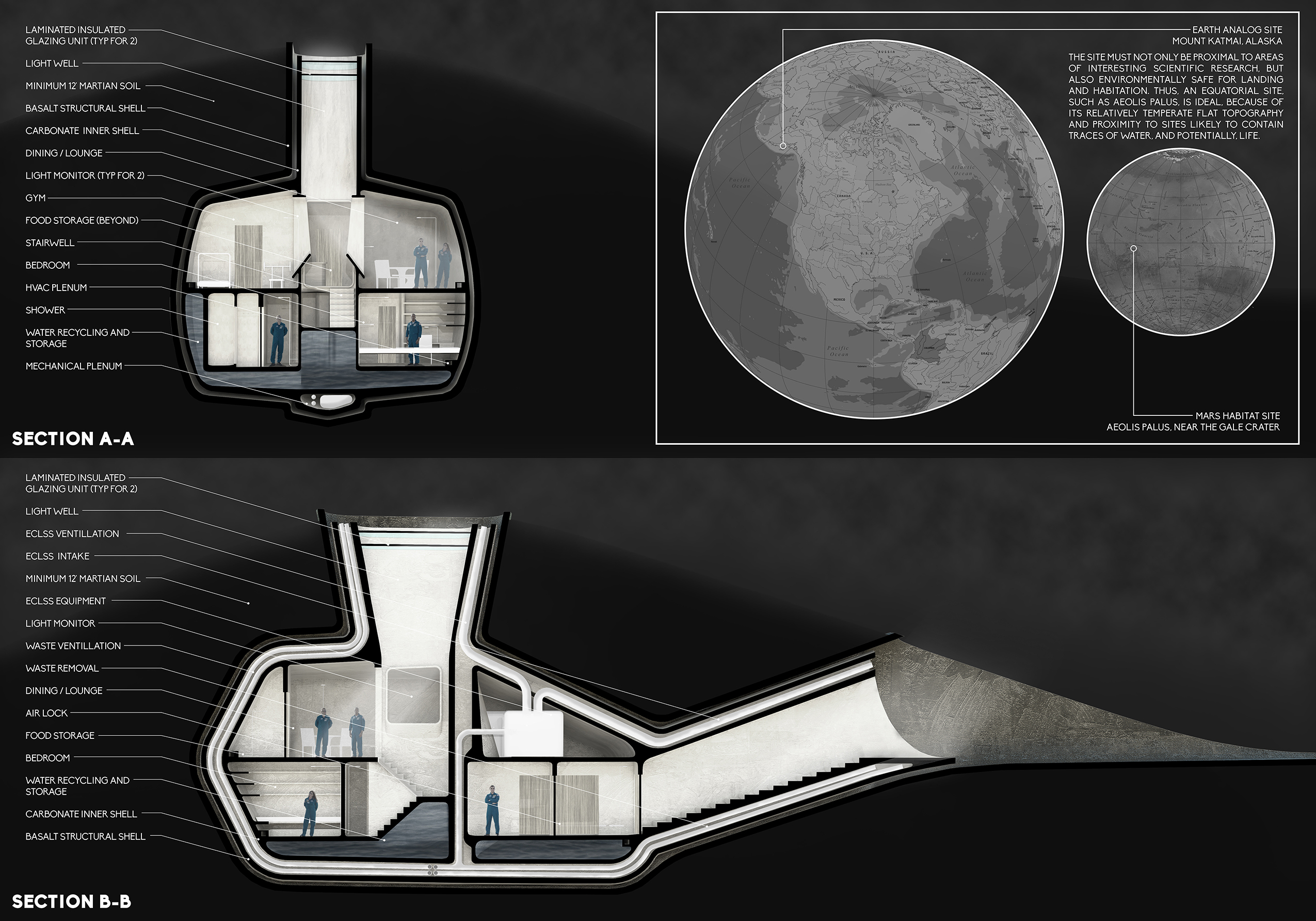
Because Mars’ thin atmosphere and lack of a magnetic field leave the planet’s surface vulnerable to harmful solar radiation, much of the organizational strategy of the habitat is focused on radiation shielding. The volume is divided into two floors, with spaces located according to time of occupation and sunlight dependencies, and the entire structure is submerged below the surface of the Martian soil. The first floor contains areas that are occupied for extended periods of time and do not require sunlight for atmospheric comfort, including bedrooms, medical and geological research facilities, restrooms, and the extravehicular activity (EVA) staging room, as their depth below grade will provide radiation shielding equivalent to that of Earth’s atmosphere. The upper level contains social spaces that are occupied for relatively short periods of time, including the kitchen, dining area, gathering spaces, and the gym, and will trade somewhat reduced shielding for access to indirect light through deep roof monitors.
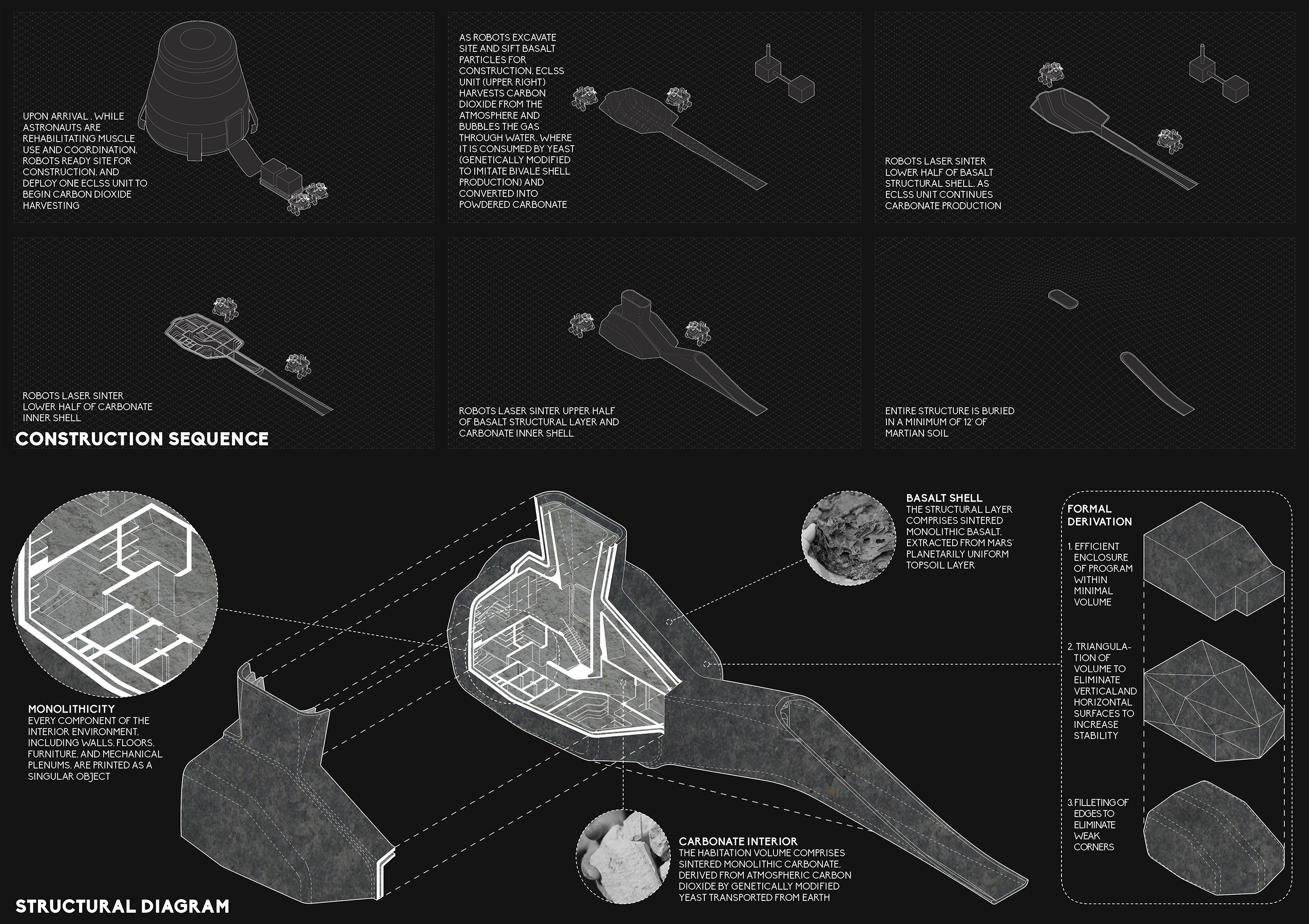
The building must act both as a structural and environmental enclosure that can support the weight of ten-to-fifteen feet of martial soil and protect from harsh temperature shifts and weather systems, and as a comfortable pressurized environment in which the astronauts can thrive. Thus, the habitat is made from a two-part material composite consisting of a rough but sturdy basalt exterior and a smooth white carbonate interior. Its structural form takes advantage of the unique load-bearing qualities of mathematically derived minimal surfaces, which would be prohibitively difficult to build without large-scale additive manufacturing techniques.

While material from the exterior shell can be sifted from the mafic-rich topsoil, the carbonate will be derived from atmospheric carbon dioxide via a process that includes the habitat’s in-situ resource utilization system (ISRU) and genetically modified baker’s yeast, the only material involved in the building process that will require transport from Earth. The ISRU will pull carbon dioxide from the atmosphere and pump it through liquid water occupied by yeast that has been modified to express genes active in bivalve mollusks. This yeast will convert the carbon dioxide to carbonate powder at room temperature with a yield of approximately two pounds of carbonate for every pound of carbon dioxide.

For the monolithic printing of both materials, we propose a fully automated laser sintering system that delivers and thermally fuses the powdered build material simultaneously via a single printhead mounted to a robotic arm.This process will be powered through the habitat’s nuclear fission reactor, solar cells, or both. While other additive manufacturing systems require large amounts of binding agent, buttressing matrices, or beds of support powder, this system is self adhering and self supporting, thus the only necessary materials are the printer and the printing material, and the structure does not need to be excavated after assembly has finished. While other additive manufacturing systems require large amounts of binding agent, buttressing matrices, or beds of support powder, this system is completely self-adhering and self-supporting. The only requirements are the printer itself and the in-situ building materials.
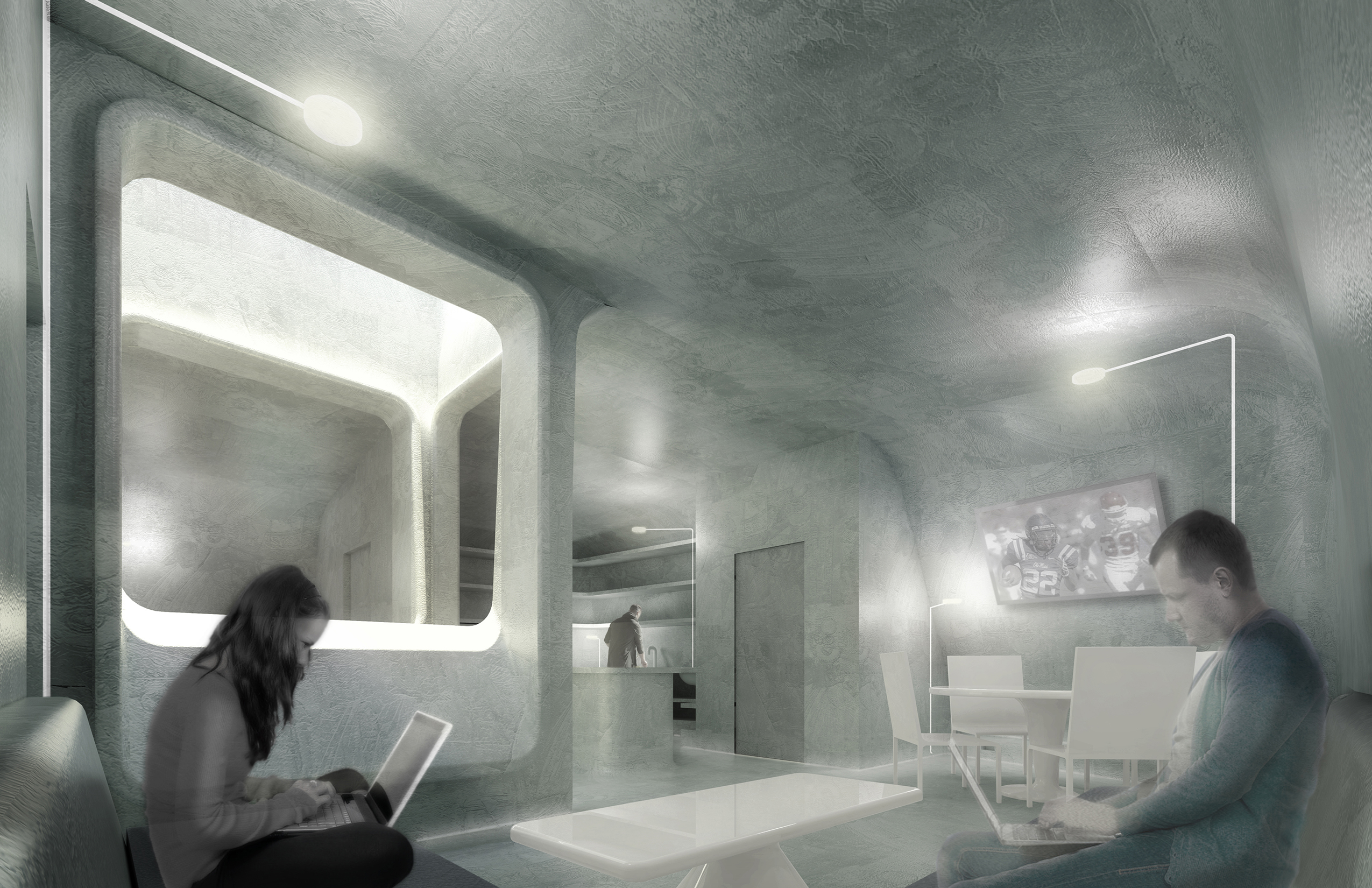